-
What is PPE?
-
Types of Personal Protective Equipment
-
Respiratory Protection
-
Skin and Body Protection
-
Eye Protection
-
Hearing Protection
-
Summary on PPE Categories
-
When is Personal Protective Equipment Needed?
- OSHA Standards for Personal Protective Equipment
-
PPE Storage
-
Training for Employees
-
COVID-19 and Personal Protective Equipment
-
PPE for Construction Sites
-
Hard Hat Selection
-
Last Step in the Hierarchy of Hazards
-
PPE Requirement Signs
-
Personal Protective Equipment is Effective
PPE is essential for every job that involves employees working in dangerous environments or alongside hazards. However, picking the right PPE for unique situations can be confusing and difficult due to the sheer number of possible situations and combinations of PPE available. This lengthy article is here to lay out the basics of choosing and implementing PPE practices that not only protect workers, but also prolong the life of those pieces of personal protective equipment.
What is PPE?
Personal protective equipment, also known as protection equipment, PPE, safety gear, or protective gear, is any type of clothing or equipment worn by a person to keep them safe from workplace specific hazards. Typically this is protection from any physical, radiological, electrical, chemical, biological, mechanical, or any other threat in the workplace.
PPE is the last form of defense for employees while working in hazardous environments. This article will go into that particular concept later in much deeper detail, but it is prudent to know that there should be safety measures in place that mitigate or eliminate workplace hazards entirely to provide an extra level of safety for workers. Think about it this way, no woodworker would ever skip out on using safety goggles even if there was a safety trigger on their nail gun. Accidents can happen and PPE can be a lifesaver in most every instance.
There are several regulations that dictate when and where PPE is necessary, most of them are outlined by OSHA. Besides mandatory regulations put in place by OSHA, there are also industry standards, or best practice methods, outlined by standard setting organizations such as the NFPA or ANSI. These guidelines provide users with additional recommendations for proper PPE use within their own field of expertise.
Types of Personal Protective Equipment
Section 1910.132(h)(1) in OSHA’s general requirements regarding PPE, specifically states, “…the protective equipment, including personal protective equipment (PPE), used to comply with this part, shall be provided by the employer at no cost to employees.” This refers to specialty equipment that will not be used outside of work. With that being said, some pieces of protective gear such as steel toed boots or ordinary clothing that protect employees from weather are not required to be purchased by the employer. This is because these items are classified as non-specialty equipment that can be used in every-day activities outside of work. Both specialty and non-specialty protective gear must be chosen and approved by employers to ensure employee safety in the field.
Aside from non-specialty PPE, there are numerous types of personal protective equipment available that are used to improve overall workplace safety for individuals. Some of those categories include respiratory protection, skin and body protection, eye protection, and hearing protection. The following sections cover those four categories, the PPE options within them, and regulations and standards to look to for advice.
Respiratory Protection
Respiratory protection measures are essential in environments that contain dust, debris, and hazardous chemicals. If not properly protected from these hazardous airborne conditions, employees may severely damage their lungs to a point that results in permanent impairment. For this reason, it is critical for employers to be familiar with OSHA’s respiratory protection standard—CFR 29 1910.34.
There are two main categories of respirators, each with a slight variation:
- Air-Purifying Respirators (APRs) – An APR pulls air from the surrounding environment and actively works to filter out contaminants.
- Powered-Air Purifying Respirators (PAPRs) – These, while still using the same filtering principles as an APR, are powered in a way that assists the wearer in breathing through filters.
- Supplied Air Respirators (SARs) – A SAR pulls clean air from a contained source of oxygen.
- Self-Contained Breathing Apparatus (SCBA) – These work the same way as a SAR system but there is a finite supply of oxygen.
Properly functioning Air-Purifying Respirators rely on the user choosing the correct cartridge for filtering out gases and vapors OR special particulate filters to prevent the user from breathing in larger debris. As a quick review, gases and vapors include:
- Volatile organic compounds
- Noxious gases such as ammonia, mercury, or hydrogen cyanide
Respirator cartridges are classified by color. Choosing the right color corresponding to the correct sorbent for absorbing these toxic gases is essential for the safety of all workers. Failing to do so can result in serious injury or even death.
Aside from gases and vapors, larger solid or liquid particulates requiring filters include:
- Metal dust, organic dust, asbestos
- Fumes
- Mist
- Radon daughters
Once the type of toxic substance is verified and the correct cartridges or filters have been identified, the employer must now determine the size, class, and efficiency levels appropriate for their unique working environment. The size must be considered first, there are two types available:
- Tight fitting respirators – These require a fitting to properly protect the user. If there are any leaks within the apparatus, then the user could suffer from breathing in unfiltered air. There are four different options for tight fitting respirators:
- Quarter masks that cover the nose and mouth
- Half-face masks that cover the nose to below the chin
- Full facepiece masks that cover from below the chin to up over the eyes
- Mouthpiece respirators used only for evacuation purposes. These fit in the wearer’s mouth and includes a clip that keeps the nostrils closed
- Loose-fitting respirators – These do not require fit testing as the user is typically covered from head to toe in a suit. There are two types of loose-fitting respirators to choose from:
- Hoods or helmets that cover the entire head
- Face shields with rubber or fabric sides
Fit testing or not, both size categories of respirators need to go through either what is called a qualitative fit test (QLFT) which uses the wearer’s sense of taste and smell to detect leaks, or a quantitative fit test (QNFT) which uses a machine to measure leaks. Both of these testing strategies must use OSHA approved protocol to be compliant.
Next comes the class of filter and its subsequent efficiency levels. There are three classes of filters available to choose from:
- N-Series: Not oil resistant and must only be used for solid and water-based aerosols.
- N100 is 99.97% efficient
- N99 is 99% efficient
- N95 is 95% efficient
- R-Series: Oil resistant and can work with any particulates. They are only viable for one eight-hour shift.
- R100 is 99.97% efficient
- R99 is 99% efficient
- R95 is 95% efficient
- P-Series: Oil proof and can be used with any particulate matter. The length of use is determined by the manufacturer.
- P100 is 99.97% efficient
- P99 is 99% efficient
- P95 is 95% efficient
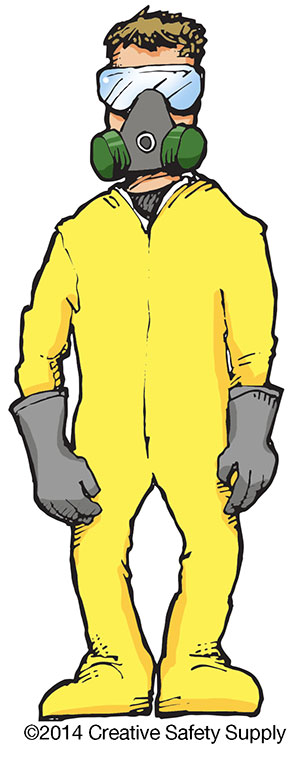
There’s a lot that goes into choosing the correct respirator for employees. Being sure to know all the restraints and capabilities is the first step in choosing, and therefore protecting, all employees from present health hazards.
Skin and Body Protection
Chemicals, physical objects, biohazards, heat, and electricity all have the potential to result in serious injury, illness, or death via burns, blunt force, cuts, or electrocution if workers are not using the right skin and body protection. As can be imagined, having proper personal protective equipment is extremely important when working around any of these dangers.
Hazard resistant clothing is up at the front of the line because of the countless protections different types of material can provide to their users. The following is a list of those materials and what they can do for the people wearing them:
- Wool and some treated cotton clothing are fire-resistant whereas synthetic materials are more likely to catch on fire. For example, fire-resistant PPE is important to have for firefighting operations and rescues.
- Heavy fabrics that protect against sharp objects may be helpful in instances where sharp blades in a manufacturing facility are used.
- Rubber protects the wearer from electricity, acid, and some chemicals. This becomes pertinent when a chemical spill has occurred or if there is electrical work being done.
- Disposable suits made of paper like material protect the wearer in hospital environments where biohazards and infections are commonplace while working with patients.
Clothing aside, there are other pieces of protective equipment that provide protection to the head, neck, and extremities:
- Face Shields – Face shields reduce the risk of injuries caused by chemicals or other substances being splashed into the face area. Whether working with hot items, corrosive materials, or biohazards, face shields can protect one of the most vulnerable parts of the body.
- Hard Hats – Hard hats are a great way to keep someone's head safe when working in an area where objects are prone to falling.
- Boots – There are numerous kinds of protective wear for the feet. Depending on the situation a worker is placed in, they may need steel toed boots, rubber boots, leather boots, etc. Boots have the ability to protect the wearer’s feet in instances of blunt force, slips and falls, and even save them from electrocution.
- Gloves – Very similar to boots, there are several different kinds of gloves that can be chosen from, whether that be latex, leather, rubber, cotton, or another material.
One of the more dangerous instances requiring skin and bodily protection come from the dangers posed by arc flashes in electrical heavy environments:
- Electricity-Resistant Clothing and Equipment – When working with or around high voltage areas, having PPE that can reduce the risk of electrical shock is essential. This could be rubber boots, gloves, or an entire body suit. This type of hazardous work has its own ratings for arc resistant clothing and tools that are mandated by OSHA and supported by the NFPA to actively protect workers from harm.
The standard that employers should be familiar with when regarding electrical hazards such as arc flashes is NFPA 70E. Article 130 specifically outlines the safety equipment needed to safely approach and work on electrical equipment.
Actively working to protect employees from skin and bodily damage will not only improve safety conditions within the working environment, but it will also protect the employers from large fines if an accident occurs and the correct PPE wasn’t given to employees in the first place.
Eye Protection
Protecting the eyes is extremely important because even a minor accident can cause long-term eye damage or even blindness. Thankfully, ANSI’s Z87.1 standard exists to provide guidance on picking the correct PPE for protecting this vulnerable place on the human body. This standard covers the four identified hazards that pose a risk to worker’s eyes during daily tasks, these include:
- Dust – Irritation and temporary sight impairment can occur when dust is blown into the eyes from either machinery or fans within the area. This leaves room for subsequent injuries to occur if the worker cannot see what is in their direct line of path.
- Projectiles – Any number of objects can impale the eye while the employee is working. This can either be from something flying through the air or the worker running into a sharp object. These accidents may cause permanent blindness or even death in serious instances.
- Droplets and Splashes – Preventing splashes and droplets from entering the eye is important as these can be from a number of different chemicals or even biohazards, resulting in severe illness, injury, or death.
- Radiation – Radioactive materials aren’t the only sources of radiation that can damage eyesight. The sun is also a large proponent in this kind of injury, it’s best to wear some sort of eye protection if the wearer is exposed to the sun on a regular basis.
Once the type of hazard has been identified out of those four categories, then the employer may pick the kind of protective eye wear to be used. The following are a handful of examples that are seen in industrial environments everywhere:
- Safety Glasses - Simple safety glasses or goggles provide a strong layer of protection for the eyes. This type of PPE is good for preventing objects from flying into the eyes such as sawdust, stones, and shards of glass. The wearer can even get these in a variety of styles ranging from types of lenses to the framework of the glasses or goggles.
- Welding Masks - While welding masks sometimes cover the entire face, their main function is to protect the eyes from the extremely bright light of a torch. These masks are darkened significantly to prevent the light from reaching and damaging the eyes.
- Polarized Sunglasses - This is a simple type of PPE that most people never give a second thought. If regularly working in the sun or around bright lights, wearing sunglasses can help prevent many eye conditions down the road.
Lastly, working in a facility that uses ANSI-approved eyewear must have Z87.1 approved PPE. Choosing specific hazard rated eyewear is easy because all Z87.1 PPE are labeled directly on the glasses or goggles. There are numerous different symbols that denote the level of protection a particular pair of glasses has for working in a hazardous environment. They go as follows:
- Z87+ - The glasses are rated for high-velocity impact
- D3 – Splash and droplet protection
- D4 – Dust protection
- D5 – Fine dust protection
- U – UV protection
- R – Infrared light protection
- L – Visible light protection
- Z87-2 – Prescription lenses
- W – Welding protection
- H – Designed for smaller head sizes
- S – Tinted
Choosing the correct eye protection can save the employee from excruciating pain and the employer time and money in the event of a mishap. Because of this, it is important for employers to be familiar with Z87.1 and for them to encourage and constantly remind employees of their own duties to protect themselves by wearing the special protective gear given to them.
Hearing Protection
Occupational hearing loss is common in the United States. With an estimated 22 million employed persons exposed to hazardous levels of noise and ototoxic chemicals, an extraordinary number of people are experiencing, or on the pathway to experiencing, severe hearing loss. Many people don't notice hearing damage when they are working around constant noise of a factory or other workplace. While hearing damage may not be something people realize instantly, hearing degrades over time with loud noise exposure. This is why wearing personal protective equipment for the ears is critical.
To help combat this public health issue, employers must look to OSHA and its corresponding regulatory standard 29 CFR 1910.95 that covers employee hearing protection measures. This mandatory standard lays out the decibel levels and the corresponding time restraints employees can safely be exposed to. Once those permissible noise exposure limits have been reached, employees must use some type of hearing protection that offers the appropriate level of noise dampening.
The decibel level and amount of time an employee can be exposed goes as follows:
- 90 dB - Hearing protection required if exposed for 8 or more hours
- 92dB - Hearing protection required if exposed for 6 or more hours
- 95dB - Hearing protection required if exposed for 4 or more hours
- 97dB - Hearing protection required if exposed for 3 or more hours
- 100dB - Hearing protection required if exposed for 2 or more hours
- 102dB - Hearing protection required if exposed for 1.5 or more hours
- 105dB - Hearing protection required if exposed for 1 or more hours
- 110dB - Hearing protection required if exposed for 30 minutes
- 115dB - Noise at this volume is only safe for up to 15 minutes without protection
Once the decibel level has been measured, appropriate measures have been taken to reduce the noise levels, and the amount of time the employee must spend in that environment has been determined, then the type of PPE for hearing protection can be chosen. Choosing the right PPE calls for understanding Noise Reduction Rating, or NRR. This rating measures the efficiency of different types of earplugs and earmuffs. Earplugs can reach up to an NRR of 33 while earmuffs can only reach up to 31. However, some of the best hearing protection comes from adding both types of PPE together.
The following are the different types of ear protection employees can choose from. Although, it must be remembered that within these three categories of ear protection, there are different NRR ratings to take into consideration:
- Earplugs - Earplugs are easy to use and provide a fair amount of protection by preventing loud noises from entering the ear at all.
- Earmuffs - Earmuffs go over the entire ear, and when worn properly, can provide a significant amount of noise reduction.
- Electronic Earmuffs - These advanced hearing protection devices work like earmuffs to stop the noise from coming in, but also have an electronic microphone that picks up voices and other noises and then plays them into the ear so people can still hear. The sounds are played at a low level, so they do not cause damage.
As a part of every facility’s Hearing Conservation Program, which is required by OSHA, there is the need for fit testing. Just like respirators, hearing protection must be worn correctly to provide the most effective protection against noise pollution. During this process, employees will be instructed how to wear this type of gear correctly and perform an audiometric test to ensure the right fit has been achieved. It is then the employee’s responsibility to use their hearing protection equipment to its full extent, this may require frequent reminders and further fit testing checks by employers.
Summary on PPE Categories
Overall, there are different types of PPE for just about every hazardous situation. By evaluating the hazards within the facility first, determining the type of PPE that must be used becomes easy. Remember the above was just an overview, there are ratings and specifications that must be researched thoroughly before choosing PPE for unique situations within industrial facilities.
When is Personal Protective Equipment Needed?
Ensuring employees know when they need to put on personal protective equipment is essential for their own safety. With that being said, some protective gear must be worn at all times, which makes it easy for employees to remember. Most PPE, however, is only required occasionally. Overall, PPE should always be worn where there are safety hazards that can cause harm to employees within the vicinity.
There must be clear instruction on when employees must use PPE to keep them safe, and when it is safe to take the protective gear off. These instances should be explained in training sessions for new employees and in re-training sessions with seasoned workers. PPE reminders can even come from PPE requirement signs, which will be explained more in depth later.
A good place to start when determining when PPE is required is taking a look at OSHA’s rules and regulations regarding personal protective equipment. OSHA provides excellent guidelines in this area and can help make the planning much easier for both the employer and their employees.
OSHA Standards for Personal Protective Equipment
OSHA is the authority to look to when it comes to following PPE regulations and protocol. All parts 1910, 1915, 1917, 1918, and 1926 contain a combined thirteen subparts relating to PPE. Within each subpart are several specific sections that employers need to be familiar with if they are dealing with that particular hazard. These subparts and regulatory sections are as follows:
29 CFR 1910, General Industry
- Subpart G – Occupational Health and Environmental Control
- Section 1910.94 covers proper ventilation efforts in environments that regularly use abrasion techniques to finish product.
- Section 1910.95 covers occupational noise exposure and the required PPE to protect employees’ hearing.
- Subpart H – Hazardous Materials
- Section 1910.120 covers hazardous waste operations and emergency response to incidents.
- Subpart I – Personal Protective Equipment
- Section 1910.132 covers the general requirements for PPE, equipment selection, who is required to provide it, etc.
- Section 1910.133 covers eye and face protection measures and the instances that require this type of protection.
- Section 1910.134 covers respiratory protection against vapors, gases, and particulates.
- Section 1910.135 covers the use of head protection and references ANSI Z89.1, intending for the user follow thatot consensus standard.
- Section 1910.136 covers foot protection and directs the user to comply with the requirements set by ASTM F-2412-2005, ASTM F-2413-2005, or ANSI Z41.
- Section 1910.137 covers electrical protective equipment. It also covers tools that provide protection against electrical shock as well as equipment test intervals.
- Section 1910.138 covers hand protection.
- Section 1910.140 covers personal fall protection systems and their associated equipment.
- Subpart J – General Environmental Controls
- Section 1910.146 covers confined space safety procedures, specifically ones that need a permit to access.
- Subpart Q – Welding, Cutting, and Brazing
- Section 1910.252 covers the general requirements in a setting where hot work is performed.
- Subpart Z – Toxic and Hazardous Substances
- There are too many sections to name in this subpart of 29 CFR 1910. It covers a range of toxic chemicals and protocols that revolve around each of them.
29 CFR 1915, Occupational Safety and Health Standards for Shipyard Employment
- Subpart I – Personal Protective Equipment
- Sections 1915.151-1915.156 cover the same topics as Part 1910 General Industry. However, it pertains to the maritime industry.
- Section 1915.158 covers lifesaving equipment, inspection of that equipment, and parameters for floatation devices.
- Section 1915.159 covers personal fall arrest systems including the criteria for connectors and anchorages, the type of fall arrest system that is used, and the maintenance required for it.
- Section 1915.160 covers positioning device systems, the weight requirements, and the training necessary for use.
29 CFR 1917, Marine Terminals
- Subpart E – Personal Protection
- Sections 1917.91-1917.96 cover the same kinds of topics as Part 1915 for shipyard employment. However, it pertains to marine terminals.
29 CFR 1918, Safety and Health Regulations for Longshoring
- Subpart J – Personal Protective Equipment
- Sections 1918.101-1918.106 cover the same kinds of topics as Part 1915 for shipyard employment. However, it pertains to longshoring safety.
29 CFR 1926, Safety and Health Regulations for Construction
- Subpart C – General Safety and Health Provisions
- Section 1926.28 covers the use of PPE.
- Subpart E – Personal Protective and Life Saving Equipment
- Section 1926.95 covers the general criteria for PPE in construction environments.
- Section 1926.96 covers the use of foot protection in construction environments by referencing the consensus standard Z41.1.
- Section 1926.100 covers head protection in construction environments and references ANSI Z89.1 for users to follow.
- Section 1926.101 covers the use of hearing protection in construction environments.
- Section 1926.102 covers the use of eye and face protection in construction-based environments by referencing ANSI Z87.1.
- Section 1926.103 points the user to 29 CFR 1910.134 to gather information on respiratory protection.
- Section 1926.104 covers the use of safety belts, lifelines, and lanyards and their weight limitations.
- Section 1926.105 covers the use of safety nets, the mesh size, and clearance distances.
- Section 1926.106 covers working near or over water and the necessity of floatation devices and/or buoys.
- Subpart M – Fall Protection
- Section 1926.501 covers fall protection measures in all kinds of situations pertaining to construction safety.
- Section 1926.502 covers fall protection criteria and proper protocol in construction-based environments.
- Section 1926.503 covers the training requirements associated with fall protection.
- Subpart P – Excavations
- Section 1926.651 covers excavation requirements such as emergency evacuation protocols, equipment used, etc.
- Section 1926.652 covers protective systems within excavation sites.
This long list of OSHA regulations regarding PPE may seem exhaustive, but it is essential that everything be very clear when looking to protect employees from harm. With that being said, it is important to be familiar with the regulations that apply specifically to any one environment in a facility to be able to give them the correct amount of protection.
PPE Storage
Once a facility has purchased PPE, it needs to be stored in such a way that it is kept safe but is also available to the employees when needed. Some PPE is used every day, in which case the employees may take it home with them and wear it in to work the next day. Other times, PPE is only needed in certain situations, allowing for the gear to be stored in a room or locker at work.
When taking home PPE is not an option, employees need to know exactly where to look for the personal protective equipment they need and how to access it. If the PPE is kept in a closet, make sure that the closet is clearly labeled. This can be done using an industrial label printer or a sign. Whatever the markings may be, make sure the storage area can be seen throughout the vicinity.
Aside from accessibility, it is important to make sure that the personal protective equipment is stored neatly so it is not difficult to grab and use. Gloves should always be kept in matching pairs that can be grabbed and put on quickly, pants should be folded up neatly, masks, hazmat suits, and other tools should be arranged in a logical manner.
The number one reason why storing PPE in an organized manner is so important, is because that equipment can then be examined easily during routine inspections. Inspecting PPE before and after use is particularly important because PPE that is broken doesn’t help employees in the way it should. Identifying broken or worn PPE is part of PPE care, just like storing it properly and giving employees the right training to do so.
Training for Employees
Training employees how to properly care for and use PPE is essential for all workplaces where job hazards are present. This training process must happen upon hiring the employee if their duties require donning and doffing PPE to enter the work area. Re-training can and should also happen for employees that have been there for a long time. This helps keep everyone on the same page in case any rules have changed, different PPE is made available, or if the workers just need a reminder.
Every good workplace PPE program will have the following topics covered in their training sessions:
- When protection equipment is needed and when/what articles of PPE won’t assist the worker.
- The types of PPE available to all employees.
- The right way to don and doff, adjust, and wear PPE.
- Proper PPE care including maintenance and disposal.
- How long the PPE is effective for. Consider the time limits for disposable masks and respirator cartridges.
- How to perform inspections on the PPE itself for wear or damage.
Training should also always cover how to avoid causing accidents that may require the need for extra PPE regarding cleanup efforts. Safety isn’t just a one-way road; the employees must know their responsibilities to keep themselves safe and out of danger.
COVID-19 and Personal Protective Equipment
2020’s pandemic, stretching far into 2021 already, has put strain on the PPE industry as they try to keep up with the increased demand for face-shields, N95 masks, surgical masks, and other protective gear that our frontline doctors and nurses use to care for sick patients.
The lines of PPE have been blurred regarding who generally wears this type of gear due to much of the population taking up using cloth face masks and surgical masks to prevent the spread of COVID-19. The majority of this shift is due to lawmakers mandating the use of masks in public places to try and get a handle on arresting the rate of infection as well as death in those who cannot work from home, or for running essential errands like going to the grocery store.
The following places are all examples of occupations where COVID-19 PPE is currently implemented, or will be once the establishment has been opened, to ensure the safety of employees and building occupants:
- Oil and gas occupations
- Schools
- Non-essential businesses
- Food processors
- Dentistry
- The agricultural industry
- Construction workers
- Gyms
- Retail establishments
- Restaurants
The list could go on and on. However, if these places are to reopen safely, visitors and employees need to follow the CDC’s recommendations on mask wearing, proper hygiene and social distancing measures.
PPE is not the only answer. Wearing a protective face mask is meant to work in tandem with other safety measures while citizens are out in public. The following practices are all needed to foster healthy communities and safe workplaces:
- Regular cleaning of frequently touched surfaces as well as washing hands for at least 20 seconds with soap and water
- Using social distancing
- Temperature checks
- Testing for COVID-19, isolating those who have contracted it, and using contact tracing as a means of preemptively catching those who might have been exposed
- Encouraging people to only travel when absolutely necessary
- Allowing employee to work from home if they can
Using PPE for the Coronavirus is no different than using specialty PPE in electrical environments or gear like steel toed boots. PPE is meant to be used in hazardous situations, and this pandemic is a perfect example, with the exception that it is a global concern rather than a localized accident.
PPE for Construction Sites
Construction based professions are equally rewarding as they are dangerous. Hazards around these particular environments can do severe damage to the human body without the right protective measures. Construction workers can encounter just about every hazard in the books, which is why their employers must be familiar with them as well as the PPE capable of protecting their workers from harm.
For starters, some of the most common PPE found at construction sites include:
- Body Protection – Examples of this include weather rated gear to keep employees warm and dry on the job, clothing that is resistant to fire or projectiles, and high visibility vests to ensure others are aware of their presence.
- Foot Protection – Toes are particularly susceptible to being crushed by objects. ANSI compliant foot protection is essential.
- Hand Protection – Hands are probably one of the most important tools a person has besides using their critical thinking skills. Protect these with gloves of a material that is suited for the task’s purpose.
- Head Protection – Head protection is one of those kinds of PPE that should not be forgotten. Construction environments are rife with the dangers revolving around falling objects. It’s just like riding a bike, always wear a helmet.
- Eye and Face Protection – Protecting these areas of the body from dust, chemical hazards, light radiation, and a slew of other hazardous substances is critical if maintaining eyesight and pretty looks is an important priority to you. All jokes aside, protecting the face area with goggles, glasses, face shields, or any other level of protection can save the wearer’s life.
- Hearing Protection – Those who suffer from hearing loss won’t realize it until it’s gone. Exposure to loud sounds, especially in construction sites where sound could practically knock down workers and passersby with how loud it is, can either cause sudden hearing loss or gradual hearing loss with prolonged exposure. Using the right earmuffs or earplugs is essential.
- Respiratory Protection – Dust, debris, chemicals, and vapors can all be found on construction sites. The workers need respiratory protection to stay safe from breathing these potentially toxic materials in.
- Fall Protection – As one of the more specialized types of PPE, fall protection is necessary when working from heights such as on tall buildings or bridges. A complex harness system allows the employee to catch themselves before falling from heights ranging from several feet to several stories high.
Not surprising at all, but the three most forgotten pieces of PPE are hearing protection, eye protection, and respiratory protection. Believing that you don’t need any of these kinds of PPE, even though OSHA mandates their use, is a silly notion that may have disastrous consequences.
To further outline the problem, let’s dive into how loud some machinery really is:
- Chop saw – 97-114 dB
- Chipping concrete – 102-120 dB
- Welding – 98-119 dB
- Hand power saw – 95-118 dB
Now, look back at the hearing protection section earlier in this article. Sounds at 95 decibels require the worker to wear hearing protection if they are exposed for four or more hours. All of the above tools, ones that are regularly seen in construction environments, are ones that are above that threshold of sound. Hearing loss will be imminent if earplugs or earmuffs are not used at those higher decibel levels.
Next! Eye and face protection. Not wearing goggles, face shields, or regular old safety glasses is an accident waiting to happen. Take for example, in the woodworking and construction industry there’s what’s called a “double kiss,” or more technically called a “double fire.” This happens commonly with nail guns that use contact triggers. When a nail gun misfires it can impale the user’s fingers, legs, and more applicable to this subject, become a flying projectile. Protecting one’s eyes against this type of danger can be a lifesaver. Nail guns are responsible to 37,000 emergency room visits per year, protect yourself with eye and face PPE.
Last on our list of most forgotten PPE in construction occupations are respirators. According to Johns Hopkins medicine, occupational lung diseases are preventable yet are still one of the most common illnesses within the U.S. These diseases are caused by repeated, long term exposure to substances like asbestos, which is estimated to affect around 1.3 million people in the U.S who work in the construction or industrial sectors. Other toxic inorganic dusts that can cause these problems include coal dust, and crystalline silica. Other organic dusts and particulates that cause problems include breathing in dust from hemp, flax, and cotton particulates, and breathing in fungus spores.
All these terrible outcomes for workers’ health can be avoided entirely if they are given and made to wear the correct PPE whether it be for respiratory protection, eye and face protection, or hearing protection.
Hard Hat Selection
Construction employees are subject to one of the highest rates of non-fatal and fatal traumatic brain injuries in the occupational workforce. The three primary outcomes of these instances leave workers with concussions, hemorrhages, or penetrating head wounds. These accidents can be avoided as long as workers are aware of their surroundings, avoiding falls by wearing their safety harness, and always wearing their hard hat.
There are two types of hard hats available, Type I and Type II. They are as follows:
- Type I – These only provide protection from falling objects. Type I hard hats are worn by almost every construction worker.
- Type II – These hard hats provide a higher level of protection that extends from falling objects to lateral impact. A face shield is present covering both the front and sides of the head.
Just like all other PPE, there are classes of hard hats that are rated for certain environments within those two category types. These are as follows:
- Class E – These must provide the wearer with at least 20,000 volts of dielectric protection as they are approved for working around electrical hazards.
- Class G – These are primarily used to protect wearers from impact hazards, they are the most common class that can be found.
- Class C – These also provide protection against impact hazards, but with the special addition of vents to keep the user cool in areas that could easily cause them to overheat.
Hard hats also come in various colors to provide a distinction between workers:
- White hard hats are for managers, supervisors, foremen, or engineers.
- Brown hard hats are for workers that deal with high heat such as welders.
- Green hard hats are for either new workers or safety inspectors.
- Yellow hard hats are for general laborers and those that operate machines that moves earth.
- Blue hard hats are for temporary workers, advisors, and carpenters.
- Orange hard hats are for road crews, visitors, or new workers.
Choosing the right hard hat for employees is essential to protect them from common construction work hazards. Do the research and provide them with what they need.
Last Step in the Hierarchy of Hazards
Personal protective equipment may be a very effective way to protect the lives of employees, but it should never be seen as a first line of defense. PPE is actually the last category to worry about in the hierarchy of hazards. This is because there are other ways to manage the presence of hazards without putting the employee in a riskier situation.
As a proven safety approach that helps protect employees, the hierarchy of hazards exists to provide guidance on the order of hazard awareness, mitigation, and elimination. This pyramid-like structure goes as follows:
- Elimination – When possible, eliminate all hazards completely so employees are not exposed to specific dangers. Ask questions such as, “Is this equipment necessary?” or “Does this process need to happen?” If not, get rid of them.
- Substitution – Removing one hazard and replacing it with one that is safer is an excellent choice if a hazard can’t be completely eliminated. For example, removing an outdated machine with few safety features and replacing it with a newer model that is much less risky. This is a step in the right direction for a safer workplace.
- Engineering Controls – If the hazard cannot be eliminated or replaced with something less hazardous, it’s time to think of ways that work to minimize immediate danger. This type of action can be very effective. Think about it this way, it’s essentially just containing a risk which then allows employees and the facility to be as safe as possible. For example, having any high heat processes conducted in a smaller and fire protected room will confine any risk to this one area rather than the whole building.
- Administrative Controls – Moving down the line, if none of the above can be done, or some have but there are still hazards present, the employer can use what are called administrative controls. This tactic essentially changes the way people work by implementing rules and regulations to try and reduce risks associated with a job. Take COVID-19 for example, employers are allowing employees to work in staggered shifts or even telecommute to work, therefore reducing the risk of spreading the illness via limiting close contact.
- Personal Protective Equipment – Finally comes the use of PPE. As last resort, PPE is meant to protect workers with what hazards are left after employers have done all they could to eliminate the danger. It is there to protect employees in case all the other options should fail. Being prepared for the worst-case scenario is the best anyone can do to ensure safety for their employees.
Awareness of workplace hazards is also mixed in with this pyramid of hazard controls. Letting employees know of all hazards present will better prepare them in ways regarding the avoidance of those hazards and how to properly protect themselves. Achievable in training sessions, employee awareness can be strengthened even more if labels, wall signs, and floor signs are placed strategically around the facility. These reminders can contain anything from chemical hazards present via GHS labels, machine guarding labels, and even reminders to wear PPE in certain areas.
While personal protective equipment may be the last option when it comes to keeping employees safe, it is still extremely important. PPE can reduce the risk of injury and in many cases can minimize the effect of any accident that does happen to take place. This is why using PPE is not just a requirement from OSHA and other regulatory agencies but is also a good business practice.
PPE Requirement Signs
Once it has been determined when and where employees must wear the provided personal protective equipment, it is important to make sure employees are aware of their responsibilities. In addition to providing them with training, many companies use PPE safety signs and PPE required signs to remind workers how to keep themselves safe.
There are a handful of ways to obtain these helpful safety signs, they can be:
- Pre-printed from designs directly located on sign creator websites.
- Created in-house using an industrial grade label printer, making for labels and signs that are immediately available for use.
- Custom made if a label printer is not available and there isn’t one that fits the unique situation in the options available.
PPE signs can also be made from a variety of different materials such as:
- Durable adhesive vinyl
- Aluminum
- PVC plastic
- Magnetic material
- Reflective material
- Static cling material
- Removable adhesive
OSHA compliant sign making companies like Creative Safety Supply are here to provide everything facilities need to keep their employees safe from occupational hazards. Our signs can specify when the equipment must be worn, which type of PPE is needed, and how to properly use it to protect oneself. Any and all PPE signs serve as an excellent reminder to employees for wearing the proper equipment at all times.
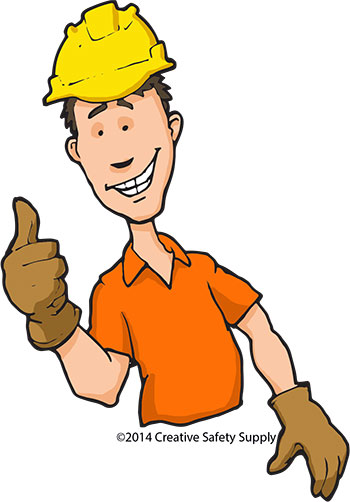
Personal Protective Equipment is Effective
Some employees may be hesitant to use personal protective equipment because they believe it would just get in the way or they tell themselves they won't get hurt even without wearing it. The fact of the matter is, using PPE is a proven way to improve safety in a facility. It’s a preventative measure that comes in handy in the rare event that something does go wrong.
Even if employees find PPE annoying or resist using it, facilities are responsible for making it mandatory. Most facilities go beyond what OSHA and other regulatory agencies require because they know just how well PPE works. In addition to keeping the employees safer, PPE allows the facility to operate more efficiently and profitably. This is due to the absence of major injuries subsequently barring employees from work, or potentially severely damaged equipment.
Workplace injuries can cause significant disruption in the flow of work and can also cost a facility a lot of money through workers' compensation or lawsuits. Even in cases where the PPE causes an initial slowdown in the way employees work, it will be worth it in the end. The improved safety of the facility more than makes up for any temporary loss in production speed that may occur when adding or expanding the use of personal protective equipment in a facility.
All facilities need to make sure their policies regarding personal protective equipment are perfectly clear and that employees follow them at all times. By making this mandatory, employees will quickly get used to the new protocol, and in most cases, find that it is actually a good addition for them and the entire workforce.
Similar Articles
- OSHA Respiratory Protection Standard (29 CFR 1910.134)
- Arc Flash PPE
- OSHA Ear Protection Requirements (Standards for Hearing Safety)
- Hard Hat Classes [OSHA & ANSI Standards]
- OSHA Construction Safety
- What is a Noise Reduction Rating? [ANSI S3.19 Explained]
- OSHA’s Guidelines to Protecting Employees from Coronavirus
- ANSI/ISEA Z87.1 Standard [Eye Protection + Safety Glasses]
- Mine Safety & Health [Expert Advice]