-
OSHA Recordable Incident Rate by Industry
-
Understanding Total Recordable Incident Rates
- The Basics of TRIR Calculation
- OSHA DART Calculator Basics
- Understanding the Lost Time Incident Rate Calculation
- Understanding the Lost Workday Incident (LWDI) Rate Calculator
- The Benefits of Safety Rate Calculators
An OSHA Incident Rate is a measure of how often a recordable injury or illness occurs at your business over a specified period, typically one year. Incident rates are a highly important metric tool that serve as a benchmark for evaluating your company’s safety program. By keeping track of these metrics, not only can you see how you measure up against other companies, but you can also set priorities for improving your health and safety performance.
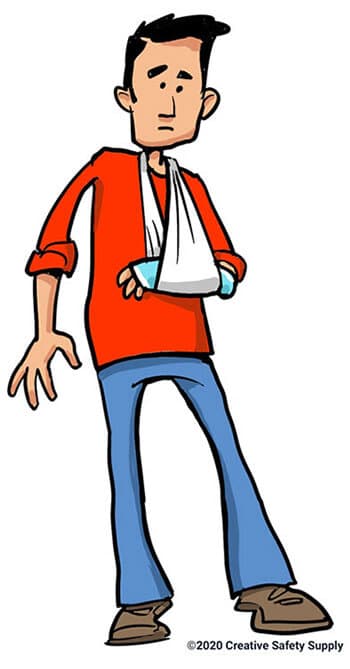
OSHA Recordable Incident Rate by Industry
The average OSHA Recordable Incident Rate varies; some industries are more susceptible to recordable illnesses and injuries than others by nature (for example, a construction site versus a marketing office). According to the U.S. Bureau of Labor Statistics, the incident rates of each private industry sector for 2020 are:
- Agriculture, forestry, fishing, and hunting: 4.6
- Transportation and warehousing: 4.0
- Arts, entertainment, and recreation: 3.0
- Health care and social assistance: 5.5
- Retail trade: 3.1
- Manufacturing: 3.1
- Accommodation and food services: 2.6
- Construction: 2.5
- Wholesale trade: 2.4
- Administrative and waste services: 2.0
- Real estate and rental and leasing: 2.1
- Other services (except public administration): 1.8
- Educational services: 1.1
- Utilities: 1.5
- Mining, quarrying, and oil and gas extraction: 1.2
- Information: 0.8
- Management of companies and enterprises: 0.6
- Professional and technical services: 0.7
- Finance and insurance: 0.3
The main causes of these incidents include sprains and strains, cuts and lacerations, overexertion, transportation accidents, contact with objects or equipment, violence, and falls, slips, trips.
Understanding Total Recordable Incident Rates
OSHA conducts investigations on companies that have high incidence rates of industrial accidents, however, the nature of the work and specific industry is also considered. Companies are compared only to others within the same industry, so “good” and “bad” rates are relative, but the general aim is to keep rates as low as possible.
These rates involve “recordable injuries and illnesses”, which OSHA defines as any work-related incidents that result in death, loss of consciousness, days away from work, restricted work, medical treatment beyond first aid, or transfer to another job.
When incident rate numbers are high, this is a red flag for a poor safety environment. Not only does your company suffer large repercussions from OSHA, but the impact will be felt across your business, as:
- Costs increase (high amount of paid time off or workmen’s compensation, hiring temporary employees, legal fees, increased insurance premiums).
- Investors lose interest and potential customers take their business to companies that have better safety records.
- Workers look elsewhere for employment where they believe they will be better taken care of.
- Quality of work decreases.
It’s important to note that OSHA Incident Rates are “lagging indicators”. This means that they indicate events from the past and aren’t necessarily representative of any procedures or incidents in the future. While they are a useful tool to measure how successful your safety program is, you cannot use them to make predictions.
The Basics of TRIR Calculation
The Total Case Incident Rate/Total Recordable Incident Rate formula considers the total number of incidents and the total hours worked by all employees within one year. There are many benefits to measuring this rate:
- Tracking this data helps improve safety initiatives.
- Potential problems can be discovered before OSHA must intervene.
- This information lends credibility to the users in the event of an inspection.
Overall, the lower the rate, the better the safety performance.
It’s important to not only understand how to calculate the OSHA Recordable Incident Rate, but also how to keep it as low as possible. Ways to maintain a low incident rate include defining your safety culture and implementing an incident investigation process; these events must be handled correctly, and it’s best to learn from your mistakes to prevent future incidents.
How to Calculate OSHA Recordable Incident Rate
The formula to calculate TCIR/TRIR is:
For many safety rates, you must calculate hours worked. The 200,000 number in many formulas is a benchmark established by OSHA to compare your own hours to, because it represents what 100 employees would work in 50 weeks based on the average 40-hour work week. It should be noted that vacation hours and leave hours cannot be included in total work hours.
An OSHA Incident Rate calculator makes it easy to follow through with a TRIR calculation. A good TRIR rate is relative to the industry and type of work done, but once you’ve completed your calculation you can compare it to findings from the Bureau of Labor Statistics (BLS). Overall, the average OSHA Incident Rate is 2.9 cases per 100 full-time employees in private industry.
OSHA DART Calculator Basics
The OSHA DART rate is a safety metric that is commonly used by OSHA to audit high-risk industries. This rate is also a useful tool for EHS managers, who can use DART to evaluate the type of impact injuries or illnesses make on a business over time.
What is a DART incident? These are occupational injuries and illnesses that specifically result in “Days Away, Restricted, or Transferred”; employees end up remaining away from work, restricting their work activities, or transferring to a different job location within a year.
For example, an employee may have sprained their back while on the job and must refrain from any heavy lifting.
DART Rate Calculations
Calculating the OSHA DART rate involves a formula that defines the number of recordable incidents that resulted in days away, restrictions, or transfers per 100 full-time employees.
A good DART rate is ideally lower than the TCIR/TRIR rate a company possesses. The BLS reports an average DART of 1.5 for every 100 full-time workers in the private industry. A key factor to lowering DART rates and keeping workers safe is implementing a well-maintained safety culture.
The DART rate differs from the TCIR/TRIR rate in that it includes only those OSHA recordable injuries or illnesses that resulted in days away, transfer, or restricted duty, while the TCIR calculates the number of all recordable injuries and illnesses.
Understanding the Lost Time Incident Rate Calculation
What counts as a Lost Time Incident (LTI)? Any injury or illness sustained by an employee that results in a loss of productive worktime. In this case, the worker must take time off to recover, or they must complete modified duties as they are physically unable to perform typical operations. This can range from temporary injuries that impact the employee for a few days, to permanent conditions and disabilities that prevent them from ever being able to complete the same tasks again. The most common event that leads to lost time is suffering a strain.
Lost Time Incidents provide an overview of how workforce injuries end up impacting a business’s productivity. They form the basis for performance and safety metrics such as Lost Time Injury Incidence Rates (LTIIR) and Lost Time Incident Frequency Rates (LTIFR), which calculate how many events happened throughout a specific period by hours worked or by number of employees, respectively.
Calculating the Lost Time Incident Rate
It’s common to use a Lost Time Injury Frequency Rate calculator to understand the impact of Lost Time Incidents on your company. The LTIFR formula is:
The LTIIR formula is:
As with other incident rates, a good Lost Time Incident Rate is one that is as low as possible. Ideally, companies aim for a rate that is lower than their industry average.
Understanding the Lost Workday Incident (LWDI) Rate Calculator
Once it has been determined that an injury or illness on the job should be classified as a Lost Time Incident, then the number of “lost workdays” assigned to the case is the number of days that the employee could not come to work because of the incident.
For example, if an employee broke their wrist on Monday and had to miss the next three days, returned to work on Friday to be given limited work tasks, and missed two more days several weeks later to get their cast removed, the total number of lost workdays is five.
A Lost Workday Incident (LWDI) considers the number of days of missed work, not days that involved restricted tasks. The day the illness or injury occurred is not counted as a lost workday, and the total number possible for lost days due to a single incident is capped at 180.
OSHA Defines Lost Workday
As defined by OSHA, a “lost workday case” is a case that involves days away from work beyond the date of the onset of illness or occurrence of injury. It should be noted that OSHA no longer uses the term “lost workday” for recordkeeping. However, some employers and safety managers may find it beneficial to keep track of their LWDI.
How to Calculate Lost Workday Incident Rate
Determining your Lost Workday Incident Rate is simple with a LWDI calculator, which calculates your rate using the incident rate formula:
The Benefits of Safety Rate Calculators
Together, all these rates provide a comprehensive picture of how safe a company is. They are often used to estimate safety performance, then to develop programs and policies for future prevention.
Using a one-stop safety rate calculator that includes lost time cases, lost workdays, DART cases, total recordable incidents, and total hours worked is an effective way to evaluate safety and take into account several different factors that may influence incidence rates.
Reducing the Injury Frequency Rate
This rate measures how many injuries there are in a period of time. In many cases it is a good general indicator of a workplace’s health and safety environment.
There is a difference between the frequency rate and the severity rate of injuries. The frequency is how often incidents occurred, while the severity is measured using the number of days of work lost. The formulas are:
Injury frequency rate:
Injury severity rate:
Reporting the OSHA Incident Rate
It’s important to maintain safety paperwork and adhere to regulations about recording and reporting incidents. There are three forms for reporting the OSHA Incident Rate that employers need:
- Form 300, “Log of Work-Related Injuries and Illnesses”
- Form 300A, “Summary of Work-Related Injuries and Illnesses”
- Form 301, “Injuries and Illnesses Incident Report”.
In 2016, OSHA published a final rule stating that establishments with 250 or more employees are required to submit form 300A only, rather than all three. The agency also requires that all businesses, no matter the size or industry, maintain and keep 300, 300A, and 301 forms for five years.
Summing Up: Recordable Incident Rates
The aim of using OSHA incident rates and maintaining a successful safety program is to promote workers’ well-being. Workplace injury prevention strategies should be prioritized, and the key to this is the collection and analysis of data such as incident rates.
By evaluating your company’s safety performance and focusing on prevention, operations will continue to be successful as workers are kept happy and healthy.
Similar Articles
- Understanding the OSHA 300 Log and Other Incident Paperwork
- OSHA Accident Reports
- OSHA Facts [Updated Statistics 2019]
- OSHA’s Guidelines to Protecting Employees from Coronavirus
- OSHA Construction Safety
- OSHA Card [Program Requirements + Benefits]
- Workplace Safety Inspections & Audits
- Fall Protection in the Workplace: OSHA’s Guidelines
- Occupational Safety and Health Administration