Often referred to as just "Lean," the Lean manufacturing method approach has been implemented in businesses and organizations across countless industries. It can be found being used in work settings such as manufacturing, healthcare, offices, and government. Within those industries, Lean manufacturing’s main objective is to improve processes and reduce waste, which can be achieved easily and efficiently by involving employees in all aspects of the organization. This method takes on an all or nothing stance in continuous improvement—everyone must participate for it to be successful in the end.
What is Lean Manufacturing?
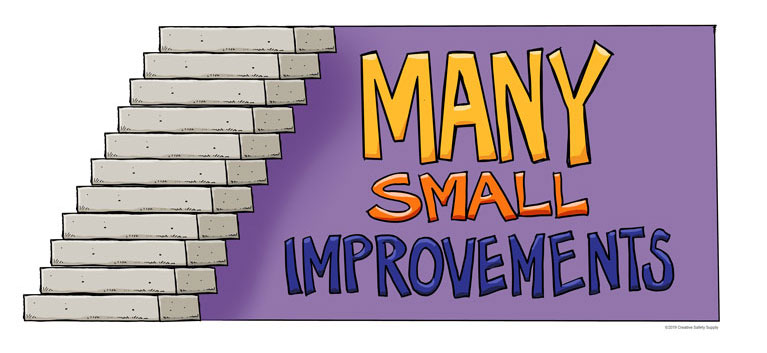
Lean manufacturing is a strategy that seeks to deliver high-quality products or services to customers as efficiently as possible. Generally, Lean works to ensure value by identifying waste within the value stream and then proceeds to eliminate that waste whenever possible. Businesses that employ this strategy strive to proactively seek possible chances for improvement at all times.
When people hear the term Lean, they often worry it means eliminating people, that is not the case. In Lean, people are what make the system work and respect for those people is an integral part of Lean. Overall, rather than seeking to eliminate people, a Lean workplace should seek to eliminate waste. If a task is eliminated, the person who performs that task should be reallocated elsewhere rather than let go.
Organizations that decide to adopt Lean must first understand the origins and goals of this methodology. Then, employers must provide the necessary training to transform the culture of the workplace to reflect those Lean objectives. This is not a system that can be implemented overnight, but when businesses spend time on Lean, they often see significant increases in productivity, efficiency, and value.
History of the Lean Methodology
Lean ideas have appeared in industry for centuries. In fact, it began with the shipbuilding industry in Italy in the 1450s, but the very first rendition of what is known today as Lean manufacturing began with Henry Ford's auto plants in the early twentieth century. Ford’s success boiled down to having equipment placed in the order it was utilized. The goal was to create facility efficiency through a continuous process flow.
While Ford’s new auto production methodology worked well for a time, this production process didn’t provide the capability of variety that the public wanted—back then, the Model T only came in one color and all had almost identical interiors. However, other leaders within the Lean production industry molded this method into an even more efficient and profitable process with small improvements that created a landslide of success in future Lean factories.
The Toyota Production System
The pioneers of the new and improved production system were Kiichiro Toyoda, Taiichi Ohno, and others at the Toyota Motor Company in Japan. They revisited Ford’s attempt at efficient process flow production in the 1930’s and created what is known today as the Toyota Production System, or TPS. By making improvements to the original idea that Ford put forth, Toyota was able to make itself more competitive, streamline processes, and provide the public with the variety of products they demanded.
There are fourteen principles that belong to the Toyota Production System and those include:
- Basing management decisions on long-term philosophy
- Revealing problems needing to be fixed by creating a continuous process flow
- Avoiding overproduction by using a “Pull” system
- Leveling out workloads
- Producing quality product the first time by implementing a continuous improvement culture
- Standardizing tasks
- Using visual control
- Using reliable technology
- Encouraging the growth of leaders who will pass on knowledge
- Developing people that will follow the company’s philosophy
- Respecting partners by challenging them and helping them improve
- Using Gemba
- Making consensus decisions
- Becoming a learning organization
The Toyota Production System puts an emphasis on respecting people, eliminating unnecessary waste within all processes, and continuously improving the workplace. If these improvements were haphazardly attempted set goals would ultimately fail.
Goals of the Toyota Production System
Overall, the goals that the Toyota Production System has includes:
- Eliminating waste
- Streamlining processes
- Increasing efficiency
- Improving productivity
- Respecting people
- Pleasing the customer
By conforming to the fourteen principles, these goals have the chance to be fulfilled. Again, all employees, even those in management, need to participate in this grand effort for improvement— otherwise objectives will fall flat and goals will not be reached.
TPS + Lean Manufacturing
The term "Lean manufacturing" emerged in the late 1980s among researchers, writers, and consultants who had studied the way automobiles were produced in Japan. In fact, several books published in English in the nineties helped spread TPS ideas around the world, and today, companies in a wide variety of industries and countries utilize Toyota's methods.
It must be noted that the Toyota Production System directly influenced the creation of Lean manufacturing. The two systems are similar but different in that Lean manufacturing puts the customer, workflow, accuracy, and relationships first while TPS puts respect for employees and continuous improvement first. Many of the same components as waste elimination and Continuous improvement are present in both strategies, but each of their priorities are slightly different. Lean manufacturing was intended to be the generic version of TPS for businesses to learn and implement into their own facilities. As time went by the interpretation of Lean manufacturing morphed into what it is today
Understanding the Lean Manufacturing Principles
There are five primary principles to Lean Manufacturing that exist to guide those that wish to implement Lean manufacturing within their own facility. Those Lean principles include:
- Defining value – Value is what a customer is willing to pay for a product. For companies to gather information on what that customer wants, they must conduct surveys or interviews.
- Mapping the value stream – The goal here is to use the customer’s value specifications as a reference point for identifying the necessary steps to get there. There are two forms of waste that should be identified and either eliminated or improved upon, and those are non-value-added waste that is necessary and non-value-added waste that is unnecessary.
- Creating flow – After the above waste is removed from the process, the facility must focus on ensuring the steps run smoothly. Training employees that can do several tasks, breaking down and reconfiguring production steps, and improving workloads can help with this.
- Establishing pull – Here the goal is to have just enough inventory and WIP items to create a smooth process flow. This strategy is also known as a Just-in-Time production process.
- Aiming for perfection – All employees must strive to perfect the above four principles to change the work culture into one that prioritizes continuous improvement. This is arguably the most important objective of all.
DOWNTIME: 8 Wastes of Lean
When TPS was first created there were only seven wastes that were recognized. However, with the gradual changes that came with Lean manufacturing, there was one more waste added to the list to help production facilities a little bit more in improving working conditions in terms of efficiency. That waste is known as non-utilized talent.
With the new addition of this eighth waste there came an easy acronym to remember, and that is DOWNTIME. The acronym, a symbolic plague of many industrial facilities, is the perfect descriptor for these eight wastes as wasted time is at the core of every single aspect within these problematic situations of manufacturing.
The eight wastes of Lean include:
- Defects - Products or services that cannot be sold due to not meeting company standards
- Overproduction - Producing too much product without demand
- Waiting - The down time between production process steps
- Non-utilized talent - Not using the full capabilities of employees
- Transportation - Unnecessary movement of materials
- Inventory - Storing more product that contributes to slow turnover and wasted money
- Motion - People or equipment moving more than what’s needed in the production process
- Excessive processing - Steps that don't add value to product but cost resources
What is Muda, Mura, and Muri?
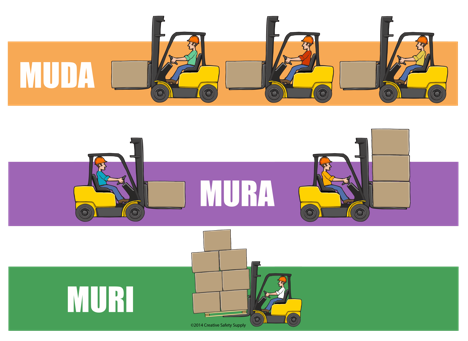
Muda, Mura, and Muri were introduced by the Toyota Production System and later used in Lean facilities as a basis for recognizing and eliminating wasteful practices within a company. In Japanese Muda means waste, Mura means unevenness, and Muri refers to overburdening employees or equipment.
To begin, Muda can be split into two categories of waste— non-value-added activities that are necessary for production and non-value-added activities that are not necessary within the manufacturing process. There is a similarity here with TPS’s version of waste and Lean’s version of value stream mapping. Regardless, that second version of waste needs to be eliminated. The acronym TIMWOOD is a good resource to use when identifying waste that must be eliminated. It stands for:
- Transport
- Inventory
- Motion
- Waiting
- Overproduction
- Over-processing
- Defects
TIMWOOD is essentially another way of looking at DOWNTIME, just without the non-utilized talent present in the eight wastes of Lean. With that being said, these seven wastes recognized by TPS must be eliminated to improve facility efficiency.
Next is Mura, which is defined as unevenness. Mura is the catalyst to Muda, in other words, unevenness and irregularities in production cause waste that manifests in areas such as over processing, too much inventory, waiting, motion, etc. Eliminating areas of waste will help Mura but using pull based strategies or Kanban can further enhance efficiency to improve TPS and Lean management techniques.
Lastly there is Muri, which is defined as an overburden, unreasonable, or excessive expectations put on workers. Muri can be caused by Mura(unevenness) and even be caused by excessive removal of Muda(waste). By standardizing work the facility will benefit from less absenteeism, repetitive injuries, and even machine breakdowns that are caused by overburdening workers and machines.
Learning to correctly balance the elimination of these aspects of TPS and Lean manufacturing are essential for its application. These three concepts are so interwoven that it takes time to get the ratio correct in a production flow to obtain maximum efficiency. There is no right and concrete way that these three concepts can be applied to all Lean factories.
The Lean Toolbox
A Lean toolbox is a set of strategies and techniques that a company uses to help them with continuous improvement, whether that be in manufacturing or applied to business in general. There are all kinds of tools that can be applied to create a functioning Lean production facility, however, using them doesn’t mean everything becomes instantly better. In fact, using all the tools in that metaphorical toolbox doesn’t matter unless those tools are implemented and used correctly. Correct application is what determines success within Lean management.
Lean Manufacturing Tools + Techniques
Lean manufacturing has options for numerous tools and techniques that organizations can implement within their own growing Lean environment. The following are a few examples of the strategies that exist for managing people, frameworks for solving problems, and ways of structuring work.
-
Just-in-time (JIT) production is based on customer demand instead of on traditional demand forecasting. In JIT, when a customer orders product, this triggers the upstream process to begin making those products.
This method is often referred to as a pull system because production is pulled by customer orders. A pull system is preferable to a push system because it allows a business to reduce wastes such as excess inventory and overproduction. Within this system, the term takt time refers to the amount of time it takes to fulfill customer demand, while processes are then adjusted to takt time to prevent overproduction or underproduction. - Jidoka means "autonomation" or "automation with a human touch." In a manufacturing process, this could mean machines are designed so they automatically stop when something goes wrong. This way, defects are immediately detected. Autonomation also frees up people to oversee more machines at one time. Jidoka helps improve quality by catching defects so the problems that cause them can be resolved.
- Poka-yoke means "mistake proofing." Poka-yoke techniques prevent errors from occurring, and they're even common in everyday life. For example, bathroom sinks have a hole near the top to prevent water from overflowing if someone accidentally plugs the sink and leaves the water running. In a manufacturing facility, machine guarding techniques such as light curtains sense when someone is too close to a dangerous part of a machine and automatically turns it off to prevent an accident. Poka-yoke is simple, yet it prevents human error from causing problems.
- An andon is a signal that alerts people to a problem with the process. The andon could be a light that changes color from green to yellow or red to signal something is wrong. Andon boards where people post information about the status of production are also common. All of these andons help reinforce jidoka by alerting people to issues.
- Utilizing PDCA, or known as a problem-solving cycle, enables the user to easily identify and solve issues quickly. The acronym stands for:
- Plan for a specific and attainable goal
- Do the work required to reach that goal
- Check the results
- Act to amend any results that are unsatisfactory
- Gemba means “the real place” and is used to closely observe a specific process on the manufacturing floor. This gives the person performing the “Gemba walk” a chance to talk to employees who deal with the process to gather information on what exactly is going wrong. Gemba walks are great observation tools to use in a Lean toolbox because it gets to the center of where value is created within a facility.
- Heijunka levels production volumes in order to eliminate mura, also known as unevenness. This allows production to flow smoothly and efficiently. Unlike mass production where large batches of one item are made, heijunka focuses on designing processes that can switch from one product to another quickly. This is beneficial because then processes can better meet demand. In mass production, stockpiles of some products may build up while customers wait for completely different products. When heijunka is used as part of a JIT system, a process can make a small amount of one product and then easily switch to making another product to fulfill a customer's order.
- Standardized work consists of the best practices for performing a task. Ideally, standardized work is documented, and people are trained on what it is. Without standards, it's difficult to make meaningful process improvements. Standardized work is the baseline from which activities can be improved, and as such it serves as the basis of many Lean practices.
- 5S is another great strategy to add to the Lean manufacturing toolbox. The five components to 5S include Sort, Set in Order, Shine, Standardize, and Sustain. This method primarily focuses on organization, cleanliness, and maintaining those environments to help with facility efficiency, improvement of safety, and the reduction of waste. 5S is easy to implement but harder to maintain—this must be kept in mind when thinking about implementing it within a business.
- Finally, Kaizen is both a methodology and a philosophy that is fundamental to Lean. Kaizen means "continuous improvement. Once work has been standardized and production leveled, Lean still seeks ways to improve. This is where Kaizen comes into play. It can mean several things in the workplace; Kaizen iseither a short event where people focus on improving a particular task or process, or it's something performed by people on a daily basis. In the latter case, everyone looks for small ways to improve processes regularly. Over time, Kaizen becomes a mindset.
Together these techniques, and numerous others that were not mentioned, serve as the basis of TPS and Lean manufacturing. Implementing a Lean strategy stabilizes processes, makes production flow smoothly based on customer demand, identifies defects to improve quality, and ultimately it delivers what the customer needs.
Lean Problem Solving
Lean problem solving is defined in eight steps that are hands-on approaches to picking apart issues within a manufacturing process. Those include:
- Clarifying the problem
- Analyzing it
- Setting targets for improvements
- Looking for the root cause
- Developing countermeasures
- Fulfilling the countermeasures
- Checking to see if there were any changes
- Standardizing the solution to then share it
This is another great tool to use in any arsenal for Lean improvement initiatives. Problems always surface and those problems must be solved to be able to reach the goals that were put forth in the beginning of a Lean planning project.
What is Lean Process Improvement?
Lean process improvement relies on identifying opportunities within process workflow, planning on how that process can be improved upon, executing the changes, and then reviewing them with the team who works directly with those changes.
This set of four concepts doesn’t exactly tell a facility how to execute them because every facility is different and has varying needs in the ways of Lean manufacturing. In fact, Lean process improvement can be better described as a mindset rather than physical events. That also leads to the conclusion that across-the-board participation for the collective goal of continuous improvement is imperative.
The bottom line is that Lean process improvement enables a company to deliver product faster with maximum value. The toolbox of Lean strategies mentioned earlier are great ways to work at achieving that goal and completing those four concepts as well.
Similar Articles
- Kaizen and Lean Manufacturing
- Toyota Production System (TPS & Lean Manufacturing)
- 5 Lean Principles for Process Improvement
- 5 Lean Manufacturing Tools that Work
- Kaizen (Lean Continuous Improvement)
- Frank and Lillian Gilbreth: Standardization, Ergonomics, and Lean Manufacturing
- 8 Wastes of Lean [A Guide to Manufacturing Wastes]
- Eli Whitney: A Key Player in the Development of Early Lean Manufacturing
- Understanding the Principles of Lean Construction