A continuous improvement strategy is any policy or process within a workplace that helps keep the focus on improving the way things are done on a regular basis. This could be through regular incremental improvements or by focusing on achieving larger process improvements.
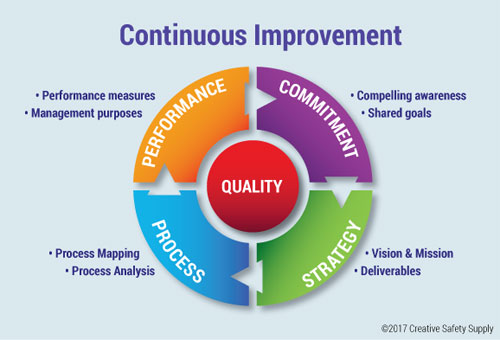
Facilities that focus on improving continuously become more competitive over time and can maintain their advantages in their industry, but only if the improvement efforts are done correctly. Taking good baseline measurements and taking ongoing measurements will help identify the effectiveness of the efforts being made.
Businesses that actively seek continuous improvement opportunities will have a much better chance at generating more value over time for both the customer and for employees. Value comes in the form of improved products, better services the business offers, better safety procedures for employees, and a sense of fulfilment in the work they are doing.
Continuous improvement is exactly what it means. Devising a continuous improvement strategy entails the creation of any policy or process within a workplace that helps keep the focus on improving the way tasks are done on a regular basis. This could be through consistent incremental improvements or by focusing on achieving larger process improvements over time.
Now that we know value is the product of continuous improvement, how does a company pursue this innovative strategy?
The Continual Process Improvement Model
There are countless ways to achieve a work culture focused on process improvement. It’s the effort involved in finding the right strategy to use for the unique industry that can be difficult Luckily, all the continual improvement models will focus on similar types of improvement, each just goes about it in a different way.
Making ongoing improvements in performance, commitment, strategy, and processes all help build up the company's bottom line. These four categories will also help improve the overall value being produced by the facility.
Facilities that focus on improving continuously become more competitive over time and can maintain an advantage in their industry. However, this is only if the improvement efforts have been done correctly. The secret is taking initial data and comparing it to data collected after changes have been made. This strategy will help identify the effectiveness of the solutions being put into action.
Improvement Strategies for Operational Excellence
The concept of continuous improvement is an umbrella term that covers many methodologies used to achieve the company’s future financial, safety, and product goals. Choosing the right improvement strategies will help maximize results and ensure long-term success.
A facility can choose to have multiple continuous improvement strategies in place at any given time. Different areas of the company, or even different departments within an area, can each work off a separate strategy to maximize results.
There are certainly more than six methods to use with continuous improvement in mind, but the ones this article will go over are some of the most common improvement strategies.
Implement the Plan-Do-Check-Act Principle
The first method on our list is the helpful concept of "plan, do, check, act,” or PDCA. This is a cyclical process that walks an entire company or small team through the four steps of improvement. By continuing to cycle through these steps, improvement is always being worked on and evaluated.
Each step builds on the previous step, and then feeds into the next.
Each step is as follows:
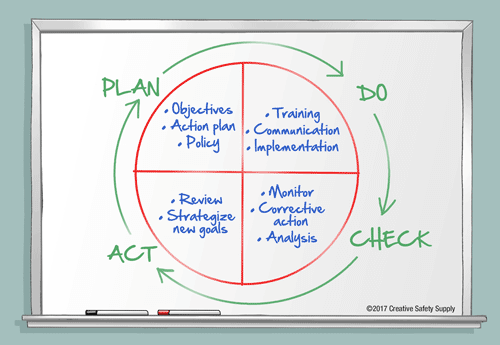
- Plan – In the planning phase, teams must measure current standards, brainstorm ideas for improvements, identify how the improvements should be implemented, set objectives, and create the plan of action.
- Do – Next, the team must implement the plan that was created in the first step. This includes not only changing existing processes, but also providing any necessary training, increasing worker awareness, and adding in any controls to avoid potential problems.
- Check – After implementing any changes, the workers must then take new measurements to compare them with those taken prior to the change. This step is essential for identifying if any improvements took place. The results must be analyzed, and any corrective or preventative actions must be planned to achieve the desired changes.
- Act - All the existing data from the change is then analyzed by management teams to determine if the change will become permanent or if further adjustments are needed. This step feeds into the plan step since once a change has been fully implemented, it is time to begin looking for new ways to make further improvement.
The PDCA cycle is an excellent example of continuous improvement because of its cyclical nature. In fact, it helps promote the idea that a process is never completely perfect, and that there is always room to improve.
Going Lean and Planning for Improvement
Wasteful practices are a huge part of inefficiencies at work. Many industries who utilize Lean manufacturing methods are familiar with the eight wastes of Lean. These eight wastes include the following:
- Defects – Products or services that don't meet company standards, therefore reducing value.
- Overproduction – Producing too much of a product than demand requires, creating the need for more storage space.
- Waiting – The downtime between steps in a production process is wasted time.
- Non-Utilized Talent – Not giving the employees the autonomy to succeed and help the organization explore new innovative ideas.
- Transportation – The unnecessary movement of materials in a production process.
- Inventory – Stocking too much inventory wastes money in terms of storage space.
- Motion – Excessive movement can involve people or equipment. This act wastes time.
- Excessive Processing – Steps in a process that don't add value for the customer but still costs the organization resources.
One easy way to remember the eight wastes is the acronym DOWNTIME.
Implementing Lean as a continuous improvement strategy allows the organization to eliminate waste throughout the facility. Again, waste is anything that doesn't add customer value.
In many ways, this continuous process improvement strategy works to eliminate problems rather than directly improve a process. The results are similar, but by taking a waste-focused approach, it is often easier to come up with goals from which improvement strategies can then be developed.
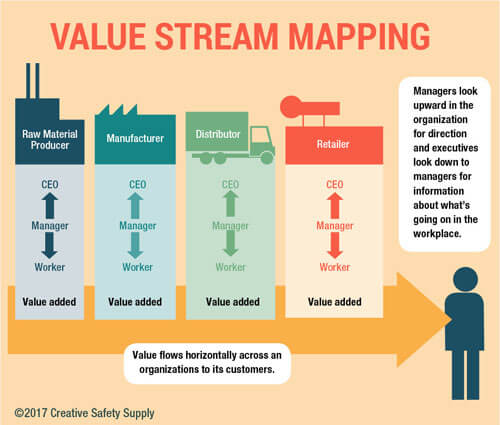
Wholistic Improvement with Value Stream Mapping
Value stream mapping is one of the most useful continuous improvement strategies because it can be used alongside almost every other method.
This process looks at the design and flow of facility processes within a business to see where value is being added. A value stream map can also be a great brainstorming tool for areas that could be improved.
A good value stream map will be very detailed and formatted like a flow chart. It is utilized to help isolate each of the steps in a process to see where value is being added and where it is not. This makes it easier to eliminate or modify the areas where value is either missing or could be increased in the process.
The idea of value stream mapping was originally developed for manufacturing processes, but it can be adapted to other industries as well.
Innovate with Kaizen
Kaizen is a popular continual improvement strategy that has been around since the 1980s. This concept helps focus on improvements that are based on making a lot of small changes rather than fewer larger changes.
What distinguishes this method from others is the fact that ideas for change typically come from the front-line employees rather than management. This is effective because those working on the front-line are directly impacted by problems and will be able to more easily identify where opportunities for improvements can be made.
Some of the benefits of Kaizen include:
- Capital Investments – By focusing on smaller, incremental changes, the company doesn't typically need to come up with significant capital resources to implement the changes.
- Engaged Workplace – By encouraging employees to contribute improvement ideas, they become more engaged.
- Long-term Improvement – Each small improvement made builds on previous improvements, leading to a snowball effect.
Standardize with Total Quality Management
Total Quality Management, or TQM, began in the manufacturing sector. It has since been adapted for use in many other environments as well. This method for continuous improvement focuses on improving employee involvement, customer satisfaction, communication, and other key elements for success within a company.
Total Quality Management is a continuous improvement strategy that is often incorporated into or alongside, other strategies to help maximize success.
Organize the Workplace with 5S
5S is an organizational method that helps identify how a workspace should be organized to improve efficiency and effectiveness. This is achieved by identifying the requirements of each step in a process and ensuring all the necessary tools are immediately available, ideally within arm’s reach.
There are many ways to do this, including:
- Organizing tools so they are easy to find
- Moving machinery around to ensure parts flow from one step to the next
- Ensuring stored parts or equipment are available when workers need them
5S is often the first method management looks to because it is seen as an “easy fix.” However, companies will often implement these changes, and then they fall behind on standardizing the new process.
Success with 5S, just like any other continuous improvement strategy, requires constant work. Nothing will change if nothing is done.
Use the Right Tools to Continuously Improve
Having the right continuous improvement tools is essential to the long-term success of any strategy. These tools can be anything that helps ensure the quality improvement process can move forward successfully.
Some simple examples of this include:
- Foam tool organizers to ensure tools are kept in good working order and stored where they are easy to access.
- Floor marking tape is excellent for improving visual communication, which can help improve efficiency and boost safety, which is essential for improvement.
- Whiteboards can assist workers and management in formulating and monitoring plans for process changes.
- Facility labels and industrial label printers can help to organize equipment, ensure employees follow safety regulations, and improve process efficiency in the workplace.
Aside from the tools that can be helpful for establishing a continuous improvement culture in the workplace, action lies in the hands of all members of the company. They must be the change that benefits both themselves and their customers in the end.
How to Implement Continuous Process Improvement
There are many strategies and methodologies available to help companies implement continuous improvement. These are a great way to start since they offer guidance on taking those first steps, as well as longer-term ideas for how to keep this strategy moving forward when it becomes more difficult.
Most companies don't strictly implement just one strategy either, but rather adapt existing methodologies to meet their specific needs. Using something like Lean as a base from which to build on can be a very effective strategy to keep a facility focused on improvement strategies today and long into the future.
Similar Articles
- Kaizen (Lean Continuous Improvement)
- 5 Lean Principles for Process Improvement
- Getting Started with Kaizen
- What is a Kaizen Event? [Planning and Execution]
- Kano Model (Analysis & Diagram)
- How to Implement 5S in an Organization
- Lean Healthcare (Principles for Improvement)
- Organizational Development Process
- Hoshin Kanri