A compliance audit is a comprehensive review of some or all aspects of the operations of a company. These reviews are typically done by third parties, especially governmental agencies, though many companies also perform internal compliance audits. These internal audits can be done either as an attempt to make improvements, or to ensure the company is prepared for the third-party audits.
In many industries, including manufacturing and warehousing, there are many audits from a variety of agencies that take place. These are intended to help improve safety both for employees of the company, and for the community as a whole.
If a company fails to meet the requirements set forth in an audit, there are often financial penalties, and in some cases, can result in a facility being shut down. Understanding the specific compliance audit requirements before they take place is an important first step in passing inspections.
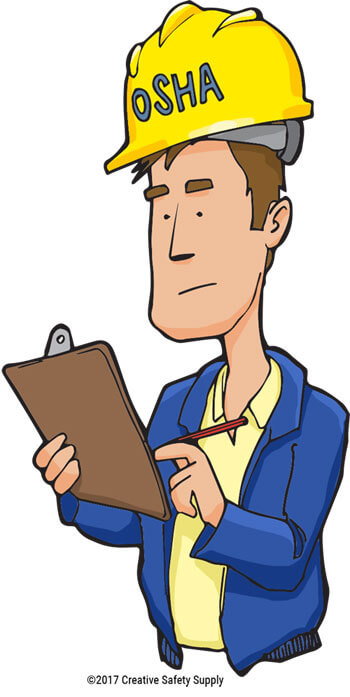
OSHA & EPA Inspections
In America, the Occupational Safety and Health Administration (OSHA), and the Environmental Protection Agency (EPA) are among the most common auditing agencies. In many cases, they work together, or perform overlapping audits. Facilities can often prepare for both simultaneously since they look at similar things.
When preparing for inspections from these agencies, companies will start by taking the time to learn about what types of requirements they have, and what they will be looking for. There are many different standards that are out there either from the regulatory agencies themselves, or from third-parties that are offering to help prepare for audits. Taking the time to find what auditors will be looking for in a particular type of facility can help ensure everything is in compliance.
OSHA 300 Logs
OSHA 300 Logs are a log of all work-related injuries and illnesses. Facilities are legally obligated to keep track of this type of information, and in many cases, submit it directly to OSHA in a timely basis. When OSHA is performing a compliance audit, they will often compare the 300 logs that they have on file with a facilities internal accident and injury log.
If there are discrepancies, the facility needs to be able to show why certain incidents were not reported. In the event that those incidents should have been reported, the facility can be fined or have other penalties.
IIPP Requirements
The Injury and Illness Prevention Program (IIPP) is a popular program that is designed to help facilities learn more about what they need to do to prevent injuries and/or illnesses from occurring due to the workplace. It also provides information about how to track and report any issues that do occur.
The program was developed in California, though it is used in many places throughout the country. The topics covered in this program include identifying who the responsible person is, ensuring employee compliance is met, understanding the requirements related to employee communication, hazard assessment, investigations, hazard controls, training, and documentation.
Safety Meetings
One of the most basic, yet effective, things a company can do to help prepare for a compliance audit is to conduct regular safety meetings. These meetings should involve upper-level management teams, front line managers, employees, and any safety coordinators or managers that work for the facility.
Having regularly scheduled safety meetings is not only important for helping to improve the overall safety of the facility, but it is also a time to go over potential compliance audit issues. Any audit issues that are identified can be addressed internally, before OSHA, the EPA, or other agencies discover them.
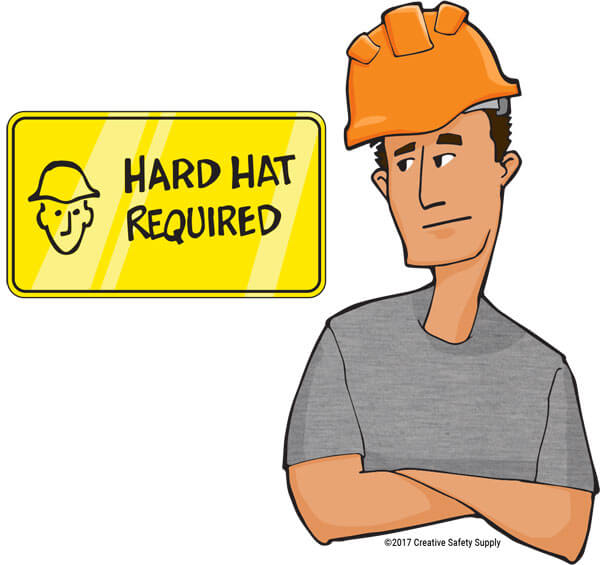
Accident Prevention
One of the main things a company can do to plan for compliance audits is to take steps toward accident prevention. This is done by identifying risks within the facility, and then implementing changes or policies in order to mitigate them. Ideally the risks should be eliminated entirely, but when this isn't possible, using safety signs or other things to ensure employees are aware of the risks can be very effective.
Any areas where serious risks for accidents are present, a facility should provide employees with personal protection equipment to reduce the severity of any incidents that do occur. The specific types of PPE that are needed will vary depending on the type of hazard that is present.
Onsite Training
Proper training for employees is another type of accident prevention effort that should be conducted. This type of training should start with new employees when they are learning their jobs, and continue as long as they are working for the company.
There are many options for onsite training including one-on-one training with a supervisor, video training courses, team training options, and much more. Each facility will need to work to identify the specific hazards that are present, and then provide training to mitigate the risks.
Multi-Facility Reporting
When a company has multiple different facilities, it is important to ensure there are safety standards that are set and followed across each one. Regulatory agencies want to see consistency throughout a company as this will show a commitment to safety.
Having any injury or illness incidents that occur reported using the same standards across multiple facilities is necessary to remain in compliance. This will allow the regulators to better identify safety issues within a company compared to trying to link them together if they had been reported separately.
PSM
OSHA does a lot to help make the tracking and reporting of any illnesses or accidents easier and more accurate. Their Process Safety Management (PSM) system is an effective way respond to hazards, or accidents, in an effective way to mitigate damage or injuries.
In the PSM publications, OSHA offers several real-world examples of different types of incidents that can take place at a facility. They then offer guidelines on how they should be handled, and what type of reporting needs to be done. All facilities that may be audited by OSHA should have a copy of the PSM on hand to refer to so that they can ensure they are following the best practices contained within.
Resources
- https://www.osha.gov/recordkeeping/new-osha300form1-1-04.pdf
- http://www.investorwords.com/19265/compliance_audit.html
Similar Articles
- Safety Audit
- Floor Marking for Electrical Panel Compliance
- OSHA Accident Reports
- Occupational Safety and Health Administration
- OSHA Sign Compliance: ANSI 1967 vs. ANSI 2011 [With 2017 Updates]
- Job Safety Analysis
- Metal-Detectable Labels for FDA Food Labeling Compliance
- What is HAZCOM? (Hazard Communication Definition + OSHA Standards)
- Organizational Development Process